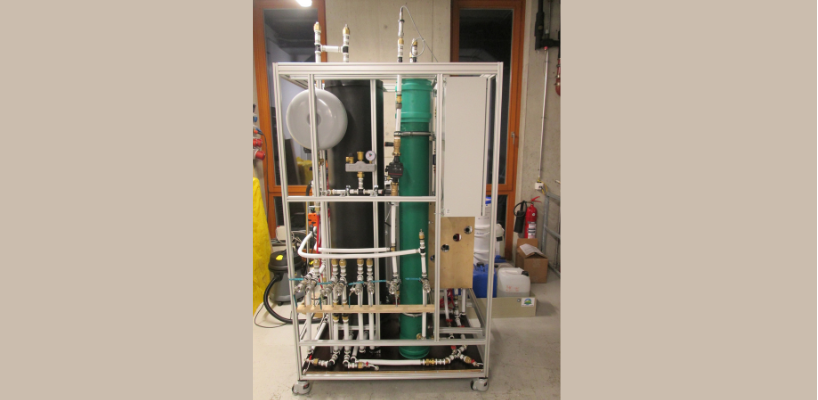
Réaliser d’importantes économies d’électricité, de CO2, grâce à l’application d’une pompe à chaleur avec circuit de réfrigération au propane dans une machine de nettoyage industrielle, c'est désormais possible. En effet, une étude réalisée par l'Institut bavarois Fraunhofer intervenant sur les systèmes d’énergie solaire ISE pour un projet « ETA dans les installations existantes ».
Le projet de recherche s'est concentré sur le développement d'un module de gestion thermique pour une machine de nettoyage de composants industriels, à la suite de ça les chercheurs y ont intégré un circuit de réfrigération au propane. « Comme les processus de nettoyage et de séchage de la machine sont effectués à de bassestempératures mais aussi élevées, il s'agit d'une application idéale pour une pompe à chaleur », annonce le chef de projet Clemens Dankwerth du Fraunhofer ISE. La gestion thermique, en veille, est couplée à la machine de nettoyage pour alimenter la machine en chaleur et en froid utiles fournis par la pompe à chaleur.
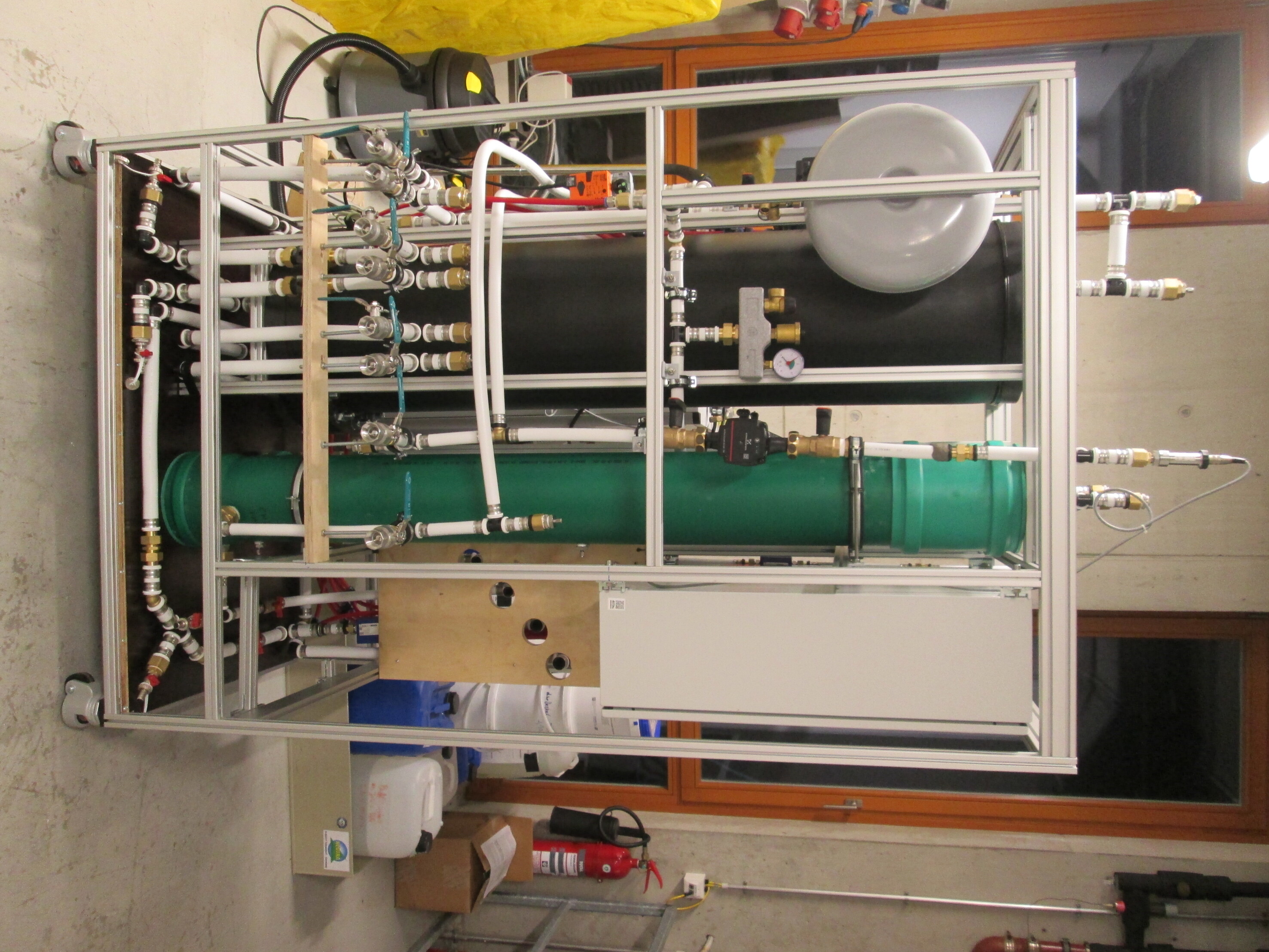
ZAE Bavière
Une basse consommation
Pour ce genre de machine, l’alimentation en chaleur et froid était électrique. Avec la nouvelle application de l’Institut, les alimentations pourraient être transférées en un seul et unique processus. Cette pompe à chaleur fonctionne de manière optimale avec seulement 255 g de propane. Ce même Institut avait déjà mis au point un circuit de refroidissement à réfrigérant réduit utilisant 150 g de propane. Les meilleures valeurs sont fournies par la pompe à chaleur, qui atteint une performance combinée de chauffage et de refroidissement de 5,6 par rapport à la puissance électrique utilisée.
Cette modernisation permet d’obtenir une plus grande efficacité énergétique. Les besoins en énergie pour chauffer l’eau et l’air ont été réduits de moitié. Grâce à la recirculation de l’air évacué, chaque année, c'est plus de 10 000 litres d’eau qui peuvent être économisées. Ces économies sont possibles grâce à la nouvelle technologie de condenseur qui refroidit l’air évacué. Dans un communiqué, l’Institut donne l’exemple « Dans une exploitation en deux équipes avec cinq jours de production par semaine et 48 semaines de production par an, le nouveau module de gestion thermique entraîne des économies de coûts d'environ 4 800 € par an et des économies d'émissions de CO2 d'environ 12 600 kilogrammes par an ».